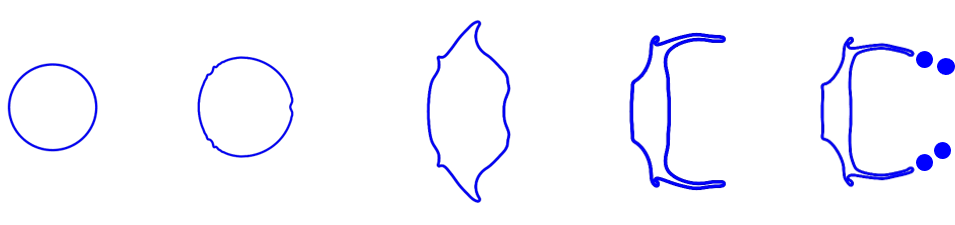
Liquid fuels have the advantage of ease of storage, higher energy density leading to higher thrust-to-weight ratios, and the ability to be used as a coolant, making them an attractive energy source for engines. In a typical detonation engine used in hypersonic applications, the liquid fuel is injected into the combustion chamber, where the high-speed gas fragments the liquid jet into droplets, called primary breakup, while the droplets may undergo further deformation and secondary breakup . As the fuel droplets deform, the high temperature environment within the combustion chamber also leads to evaporation, a process that is further enhanced by the instability-driven increase in the total surface area of the droplets due to its stretching. The fuel vapors produced from evaporation undergo combustion, thereby generating thrust and energy; thus, the overall efficiency of the engine is closely linked to the rate of droplet conversion to fuel vapors involving stretching, breakup and evaporation.
Our simulations using our in house code IMPACT address this multitude of issues, and take into account the effects of surface tension on droplet stretching, droplet evaporation and combustion. In the figures below, we show an example of a strong shock of Mach 5 strength interacting with a typical 5 micron, where we compare numerical Schlieren images from an inert droplet, a droplet that is undergoing evaporation, and a droplet that undergoes both evaporation and combustion.


Figure: The above figure shows the evolution of a liquid fuel droplet following its interaction with a strong shock. The three columns represent an inert (left), evaporating (center) and reacting (right) droplet. The top row of images correspond to early time behavior, while the bottom row of images show the droplet evolution at late times. The green outline in each image shows the outline of the initial droplet for reference.
Related Publications: