The results from the low and high-fidelity models were further examined through wind tunnel experiments. A test stand was designed and constructed to measure the torque and thrust loads. The test stand was a small-scale replica of the NREL Phase VI rotor. The generator, hub, and load cell are incorporated into the stand. This setup evaluates the performance of the blade design. EMF torque is applied to the rotor to control the speed. The scale model operated at a rotor speed corresponding to the proper tip-speed ratio of the full-scale turbine. The twist capability of the S809 blade was modeled using a set of 3D printed blades that emulated the range of TAD motion. Each shape in the set corresponds to the ideal shape found through the computer modeling (in the previous section). For each wind speed, the test compared the ideal TAD shape to the baseline model. The experiment validated the work in the previous studies. In fact, the experimental results ranged from 1 to 3% greater than those found by the low and high-fidelity models.
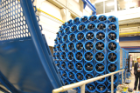
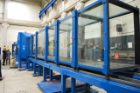